Who are Faith Guitars?
Faith Guitars are the creation of a small British team, who in the winter of 2002 had the vision of creating affordable, all-solid tonewood guitars – something that was rather uncommon back then.
Working with a small workshop of Indonesian luthiers that we believed could make beautiful guitars, the team started creating what was to become Faith guitars: the brand that has since won multiple awards and brought musical happiness to tens of thousands of guitarists.

Patrick James Eggle
In 2005 the Faith team was strengthened by the addition of renowned guitar builder, Patrick James Eggle, who was returning to the UK from the USA. Patrick moved his own guitar workshops into Faith Guitars warehouse, and a very successful partnership began.
Patrick helped re-engineer and re-design a number of key parts of the various Faith models, creating what would become ‘Series 2’ guitars, launched in 2006. Patrick has worked with the Faith team as a technical consultant ever since.
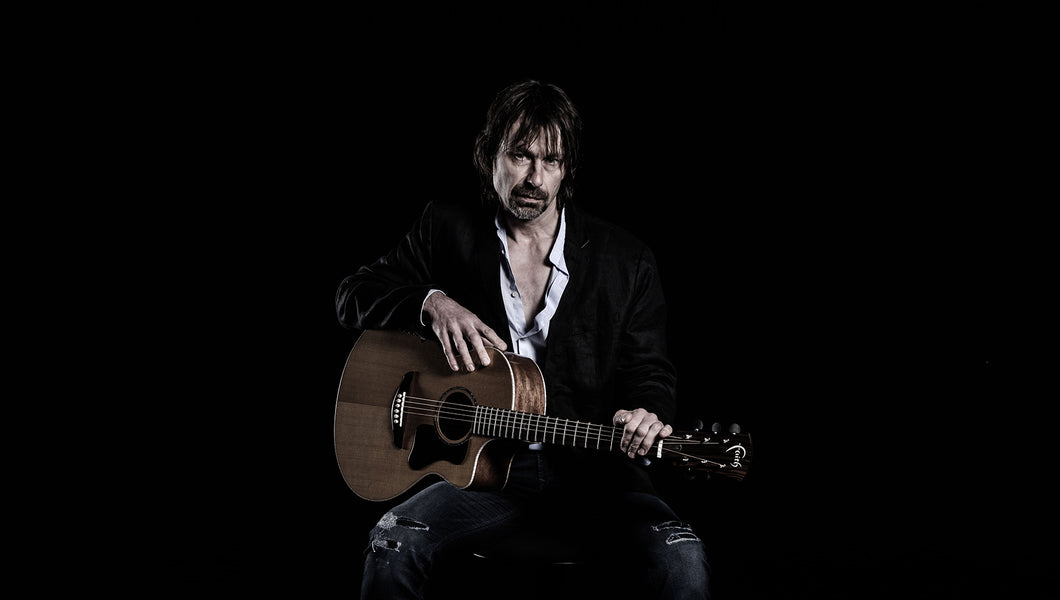
Workshop
Faith Guitars are handmade in West Java, Indonesia in a large workshop – not on a factory production line. With a staff of around 80, each guitar is given individual attention by trained luthiers who know and understand guitars. We’re very proud of our workshop, as it has produced so many beautiful guitars over the years, and continues to grow in both capacity and capability.
Having visited many times, we can confidently say that a day in the Faith workshops is just as you may imagine: production from 8:30 to 5pm in a climate controlled environment (important somewhere so hot!), with hour-long lunch breaks and a positive working style.
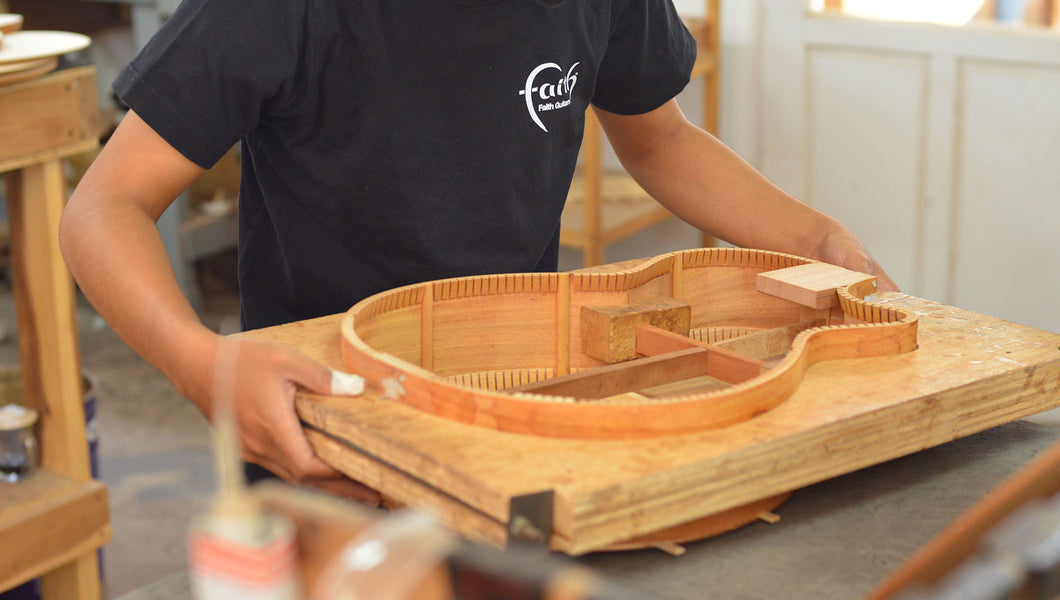
Sustainability
We endeavour to think about sustainability in all that we do. A great deal of our tonewood (Mahogany, Ebony, Rosewood, Trembesi, Mango) is locally sourced in Indonesia with SVLK certification for each package of wood purchased from timber merchants. We do not use endangered timbers, nor does the workshop purchase from unregulated suppliers.
All other timbers are purchased through well-known merchants in the USA, Canada or Spain, all of whom offer traceability to the timbers.
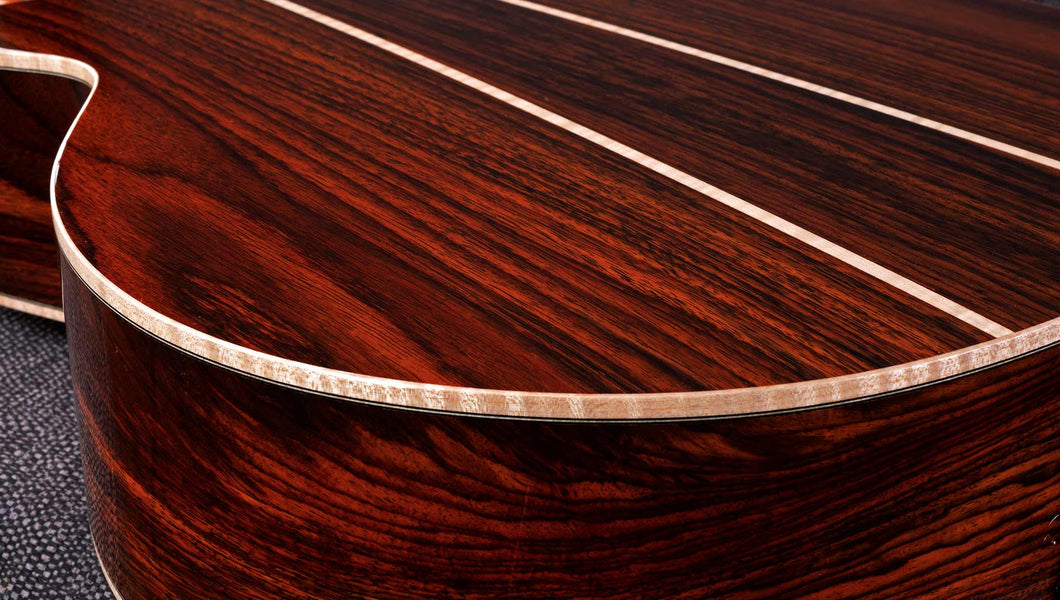
JUST ONE Tree
For the last few years, we have been proud to work with JustOneTree, a UK environmental charity who plant trees to continue the greening of our environment, plus work with local communities providing ecological stewardship training. JustOneTree was chosen for the work they do in Indonesia, so we’re able to contribute to their work in the country from which Faith Guitars sources the majority of its timbers.
We donate a proportion of the profit of each instrument sold to plant trees.
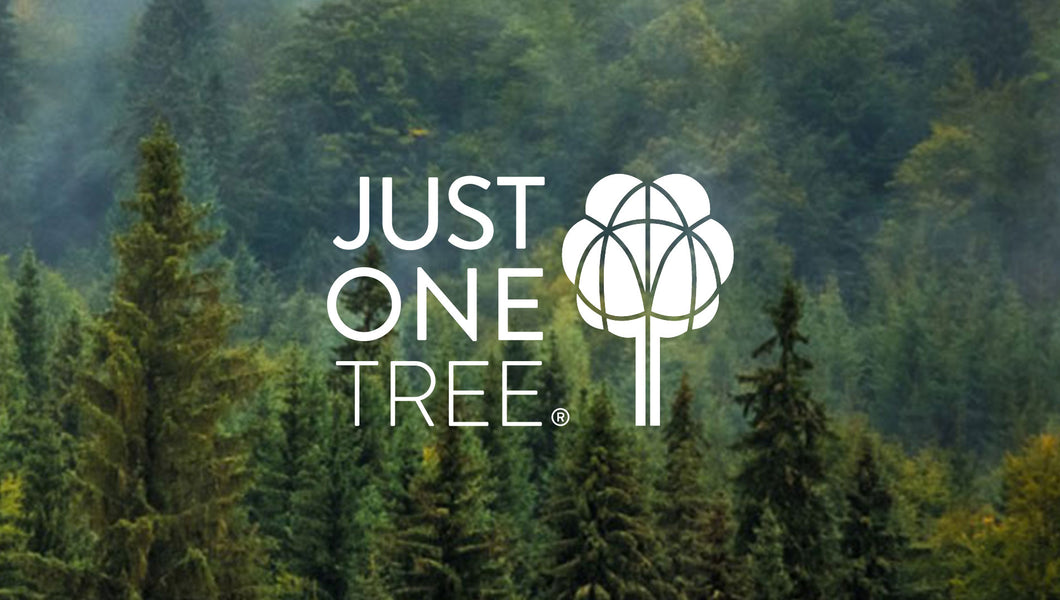